Key words: single crystal diamond tool, card bonding, damascene, brazing
Clamping and Welding of Single-crystal Diamond cutters
Zhang Jingmin
Abstract: The three technologies to clamp single-crystal diamond cutting heads on toolholders are introduced, and merits and demerits of the technologies are presented.
Keywords: single-crystal diamond cutter clamping bonding process inlaying process welding process
The rigid and reliable mounting of the single crystal diamond cutter head on the cutter bar is a key step in the manufacture of diamond cutters, and the quality of the fixture directly affects the performance of the diamond cutter. At present, there are three main types of card loading methods, namely, bonding method, mosaic method and brazing method.
1. Bonding method
The bonding method uses an organic binder such as epoxy resin or 502 glue to bond the diamond cutter head to the groove on the cutter bar that matches the size of the diamond cutter head. This method is easy to operate and does not require special equipment and fixtures to achieve a certain bond strength. However, since the temperature resistance of the organic binder generally does not exceed 200 ° C, the high temperature generated during the grinding of the cutter head or the use of a large cutting amount can cause the binder to fail, so the bonded diamond cutter is only suitable for Ultra-precision machining with a small amount of cutting, and the diamond cutter head cannot be directly ground on the cutter bar. When the tool needs to be ground, it is necessary to first melt the adhesive with a solvent such as acetone, and then re-bond the diamond head to the tool holder after grinding. In addition, the positional accuracy of the diamond tip during bonding is difficult to guarantee.
2. Mosaic method
The damascene method firstly sinters the diamond cutter head together with the metal powder, and then mechanically fixes the diamond cutter head to the cutter bar through the pressure plate. The mosaic method is currently the most widely used diamond tool loading method. The process is as follows:
(1) Roughly grind the diamond into a large and small shape and determine the position of the blade and the flank.
(2) Place the diamond face down on the cast iron mold shown in Figure 1, fill it with a proper amount of copper-based metal powder (such as 663 copper powder), then insert the upper plunger and pressurize the metal slightly. powder.
.gif)
(3) While slowly heating the mold with the high-frequency induction device, the pressure between the upper and lower plungers is continuously increased until the temperature and pressure reach 750 ° C and 5.5 kg / mm 2 , respectively. After cooling, the sintered block and the diamond cutter head therein are taken out, and a hole corresponding to the shape and size of the diamond cutter head can be obtained on the sintered block.
(4) According to the relative position of the designed blade and the shank, the excess portion on the agglomerate is removed. The machined agglomerates are then brazed to the correct position of the toolholder with a lower temperature copper braze and the rear corners and other parts of the toolholder are precisely ground.
(5) The polished diamond cutter head is placed in the hole of the agglomerate block and the appropriate pressure plate is applied to complete the loading of the diamond cutter. The installed diamond cutter head (shown in Figure 2) only exposes the flank of the tool and the rake face of about 1 mm.
.gif)
The damascene method can firmly fix the diamond cutter head, and the high temperature resistance is also good, and the flank surface of the cutter head can be directly polished after the card is installed, thereby achieving high angular precision. When grinding, just open the pressure plate, take out the diamond cutter head, and reassemble after grinding and it is very convenient.
The disadvantage of the damascene method is that the process is complicated, and the diamond cutter head can only expose a small part of the rake face, and the rear platen can hinder the chip from flowing out, which easily blocks the chip near the blade and destroys the processed surface. Since there is no chemical bond between the diamond of the insert method and the hole surface of the sintered block, only the pressure is pressed, and slight displacement may occur during the processing, so it is not suitable for the requirements of the superfinishing tool. In addition, the damascene method requires a large volume of diamond, which leads to a lower utilization of diamond, and on the other hand, it is difficult to make a small-diameter tool for small hole machining.
3. Brazing method
Direct welding of diamond tools by brazing has always been a concern. Because diamond has high chemical stability, it is difficult to chemically react with other metals to achieve welding. Therefore, how to reliably achieve the firm connection between diamond and metal has become a technical difficulty and a research topic to be solved in the diamond tool manufacturing industry.
To achieve the brazing of diamond tools, the following problems need to be solved:
(1) Wetting property: When brazing, the brazing material must wet the material to be welded to ensure that the welding site is free from defects. Due to the high surface energy of diamond and poor wettability, it has been found that solders with good wettability on the surface of diamond and metal substrates are the key to successful brazing.
(2) Bonding properties: The brazing filler metal should not only have good wettability, but also chemically react with the material to be welded to form a chemical bond to achieve a welding with sufficient adhesion.
(3) Residual stress: The thermal expansion coefficient of diamond and metal is nearly ten times different, and a large residual stress is formed during the cooling process after welding, which affects the welding strength and even damages the diamond.
(4) Corrosion of diamond: Diamond will oxidize or graphitize at high temperature. Some metals also have an effect on diamond. Therefore, it is necessary to select a suitable working environment and solder to minimize the corrosion phenomenon of diamond.
Numerous studies have found that brazing filler metals containing active elements such as titanium, zirconium, niobium and tantalum can directly wet the diamond surface in a vacuum. These active elements can also react with carbon atoms on the surface of diamond to form stable carbides, forming a chemical bond. The metal molybdenum or cobalt-based cemented carbide has a similar thermal expansion coefficient to diamond, and it can be used as a welding base to not damage the diamond and ensure the brazing strength. Based on this research, diamond brazing technology under vacuum conditions was developed. In recent years, a new technology for brazing diamond in a protective gas atmosphere has been further developed. Compared with the vacuum brazing technology, the protective gas brazing technology has the advantages of low equipment cost, simple operation, short process cycle, and the like, and maintains the welding strength equivalent to vacuum brazing. The emergence of this technology has solved the long-standing problem of diamond brazing technology more satisfactorily.
The brazing material used for the brazing diamond of the protective gas is silver-copper-titanium alloy, and the composition ratios of silver, copper and titanium in the alloy are 68.8%, 26.7% and 4.5%, respectively. The shielding gas is a mixed gas of argon (95%) and hydrogen (5%). The welding is carried out in a semi-open cavity as shown in FIG. The brazing process is as follows:
(1) sufficiently removing oxides on the surface of the diamond and metal substrate;
(2) heating the substrate and the brazing material in a protective atmosphere until the brazing material is melted and uniformly dispersed at a specified position of the substrate, and then cooled;
(3) Place the diamond to be welded in the correct part of the substrate, refill it with the shielding gas, reheat it to the melting temperature of the solder, and then slowly cool to room temperature.
.gif)
The use of brazing to mount a diamond cutter head has the following advantages: high welding strength, shear strength of the welded surface up to 340 MPa, and a diamond cutter head weighing only 0.02 carats can be firmly welded to the cutter bar; Afterwards, the diamond cutter head is further refined to ensure the machining accuracy of the cutter geometric angle; the cutter rake face can be higher than the cutter bar, thereby ensuring smooth discharge of the chips, and making the cutting process and the surface quality of the workpiece more stable and reliable; Improve the rigidity of the diamond tool system.
Phlizon`s COB series Grow Light emits all the wavelengths of light which can be fully absorbed by the plants to create.
Best full Specturm designed to perfectly match large areas of indooor plants, especially for Medical Plant.
COB + Dual-chip,most efficient spectrum,high PPFD.Two cooling fans with double ball(import from Japan) and big aluminum heat sink to protect the grow lights from high temperature,good cooling,long lifespan.Photosynthesis and promote healthy growth budding and flowering.
1000w/2000w /3000w COB LED Grow Light, it will give you more options when your plants need different strength of illumination.
Grow Lights are a great choice for growers who are dealing with hot HPS lights and want to change to something that's going to run cooler. Although LED Grow Lights do produce heat,the smaller models might not bring up the temperature of your grow space.Even the more powerful models of LED grow lights that produce a lot of heat still have built-in cooling systems to help prevent the heat from beaming directly down onto your plants.
3000w led grow light Features
Indoor grow light
COB series, high power branded CREE COB with high Par value and deeper penetration
VEG/BLOOM and STRONGER switches for each grow stage.
Special spectrum for plant growing to increase the yield.
Building to Harvest: Beneficial for seeding to fruiting stage.
Good quality fans with low noise.
Easy to install by minute
Energy Saving, environmental friendly
3 Years Warranty
Compare led grow light to traditional HPS/MH grow light
WHAT MAKE UP AN EXCELLENT LED GROW LIGHT ?
1.PPFD Value : PPFD is Photosynthetic Photon Flux Density. When you choose a plant light, you should compare the PPFD values of different plant lights. The larger the value, the better the growth of the plant.
2.Actual Power: Because the actual power of the plant light always varies with different conditions, all Amazon sellers use the rated power to describe the power of the product because the rated power is constant. When you pick a LED grow light, the rated power of the plant light is a reference, and more importantly is the actual power.
3.Core Coverage: In addition to the above two, when you choose a plant light, you also need to compare the cover area of different plant lights, of course, the size of the core coverage area. In general, in germination stage, you can hang the plant light higher and the cover area is larger. In flowering stage you can hang the plant light lower and the cover area is smaller because the plant needs more light at this stage. You have to compare different coverage areas to choose the plant light that suits you.
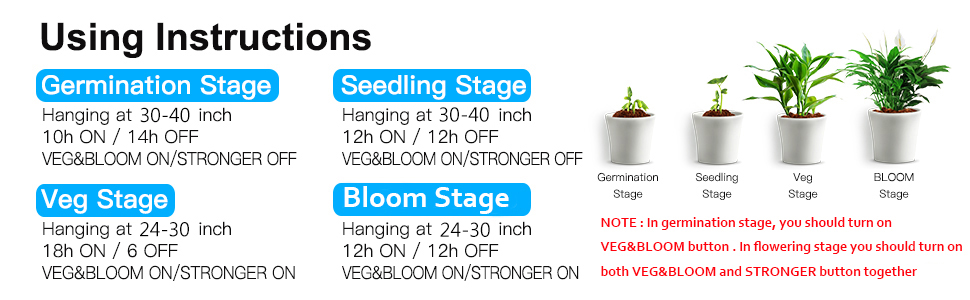
Detailed images of 1000w 2000w 3000w 400w cob led grow light
Applications
Hydroponics, Horticulture, Agriculture and Greenhouse
Locations: Farm, Exhibition, Garden, Home, Urban, Bonsai, and University Lab
Growth of Fruits, Vegetables, Flowers and so on
Seeding, Rooting, Breeding, Flowering and Fruiting period
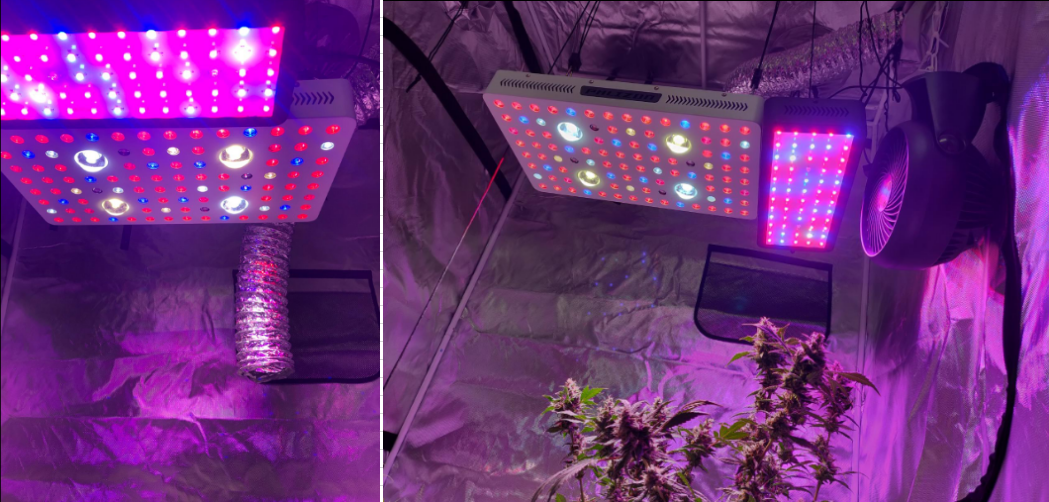
Packaging and Shipping
2. By Air or by Sea for batch goods, for FCL; Airport/ Port receiving;
3. Customers specifying freight forwarders or negotiable shipping methods!
4. Delivery Time: stock avaiable sample will be delivered immediately ; 3-7 days for trial order; 7- 25 days for batch goods
Suggestions:
1.Clean the dust inside every 6 months to ensure the good heat dissipation and long life time.
2.Don`t keep too short distance to the plant canopy to avert leaves bleaching.
3. Highly hang the lamp will weaken the energy and affect the growth cycle of the plants, so the lamp should not be hang too high.
4. While taking care of the plants, please spray the leaves and branches 2-3 times everyday, to ensure the plants do not wrinkle a wither, and have no phenomenon of few fruit, and hard pericarp
Trade Terms
Payment: T/T, L/C, Paypal, 30% deposits before production, 70% balance to be paid before deliverying(Western Union are welcome)
Sample will be delivered within 7 working days.
Discounts are offered based on order quanlityes.
MOQ:sample order are acceptable
Delivery ways:DHL,UPS,FedEx,TNT, door to door,by sea,by air,etc.
PHLIZON LOOKING FOR DISTRIBUTOR ALL OVER THE WORLD
If you are interested in, and
1.own several store for agriculture in your local market
2.or in the business of grow light equipment
3.or good relationship with grower or greenhouse owner
To be a distributor, max support will be offered:
1.price support
2.technical support
3.new product support
4.24 hours after-sales service online
PH-B-L6,Optic Cree Cob Grow Light,600W Led Indoor Grow Lights,630W Led Grow Light,Cob 3000W Grow Light
Shenzhen Phlizon Technology Co.,Ltd. , https://www.szledaquariumlighting.com