1, the generation of static electricity Static electricity is the relatively static and unipolar electric charge that the object brings, and stays on the surface of the object. It is the result that the positive charge and the negative charge lose their balance in the local area. It is formed by electron or ion transfer. The reason for the unbalanced distribution of electrons is that electrons are derailed by external forces. This external force includes various kinds of energy (such as kinetic energy, potential energy, thermal energy, chemical energy, etc.), so in daily life, such as contact, friction, flushing, electrolysis, Piezoelectric, deviation, induction, etc. will all generate static electricity.
2. Hazards of electrostatic charges on electronic components Electrostatic basic physical characteristics: the power of attraction and repulsion; potential difference between the ground and the generation of discharge currents Due to these characteristics, electrostatic discharges may cause the following damage to semiconductor devices:
1) The thin oxide layer is broken down;
2) The leakage current density is high, causing the conductor to melt;
3) Increased leakage current causing premature failure and functional breakdown of the device due to changes in breakdown voltage. Although the interior of the electrostatic sensitive device has been protected, this is only effective when the charge transfer is limited to a certain size and continues for a certain period of time. According to test reports, electrostatic discharge damage is often only 1O% causing complete failure of electronic components at the time, usually as a short circuit, open circuit, and serious changes in the parameters, beyond its rated range, the device has completely lost its specific function; 90% will lurk down, causing a cumulative effect. Under normal circumstances, an ESD is not enough to cause the device to completely fail immediately, but there will be some degree of slight damage inside the component, usually expressed as a small deviation or drift of the parameters. The potential failure is not obvious and it is easily overlooked. If such components continue to work, with the increase in the number of ESD, the cumulative effect will become more and more obvious, the degree of damage will increase, and eventually lead to failure.
With the development of large-scale MOS circuits and placement devices (SMDs) and the development of component process technology, the energy sensitivity to electrostatic discharge (ESD) increases, and thin insulation layers can easily cause damage and failure. The electrostatic breakdown voltage of various types of semiconductor devices is shown in Table 1.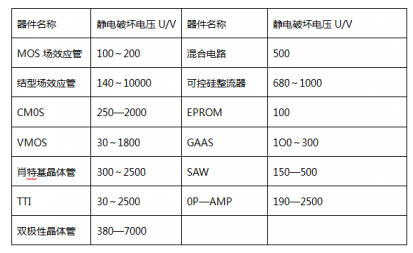
From Table 1, we can understand the sensitivity of integrated circuits to static electricity. The difference of various chips lies in the different values ​​of 闽 voltage that they can withstand. In actual working conditions, a static voltage of 20V directly contacting the device is enough to destroy or reduce its performance.
3. The harm caused by static electricity on the production of electronic products The harm caused by static electricity on the production of electronic products mainly includes the following aspects.
1) Electrostatic adsorption of dust in the air can easily lead to short circuit between the device leads;
2) Electrostatic discharge damage, so that the components can not be damaged;
3) Electrostatic discharge Electric fields or currents generate heat to damage components;
4) The amplitude of electrostatic discharge is very large. Electromagnetic fields with extremely wide frequency spectrum (from several tens of megabytes to several thousand megahertz and several hundred volts/meter of superposition) make electronic products damaged by electromagnetic interference.
5) The rework and repair of products damaged by electrostatic discharge will increase production costs and affect the economic benefits of the company.
In summary, electrostatic hazards exist in the entire process of electronic product production. The analysis result of electrostatic hazard in the production process of a certain electric shop is shown in Table 2. If the parts that are susceptible to electrostatic damage are controlled in the production process, the degree of electrostatic hazard in the production process will be limited to a minimum.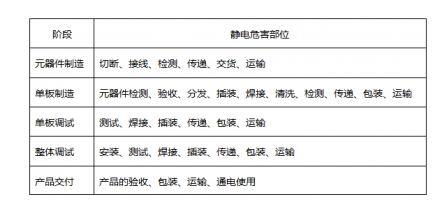
Industrial anti-static measures
1, the degree of environmental hazard control; 2, process control; 3, grounding; 4, increase the humidity; 5, antistatic additives; 6, electrostatic neutralizer; 7, to strengthen electrostatic safety management.
The most effective measure is to allow people to "connect" or "ground" with the earth. Therefore, people should wear anti-static shoes. To keep the human body connected to the earth, this requires that the ground is also anti-static, so that the static electricity of the human body can be introduced into the earth. Therefore, the ground can use anti-static mats, anti-static composite sheets, and use anti-static grounding wire to connect well, such as funds Adequate use of anti-static raised floor, especially in the planning and design of the engine room plant can consider the use of anti-static raised floor, if the computer room plant is set and the equipment has been installed, but do not want to install anti-static equipment when the production of these equipment to stop production When it is time to influence, choose an anti-static floor mat that is inexpensive and easy to construct, anti-static composite sheet, etc.
People wear anti-static shoes and have anti-static mats, anti-static composite sheet or anti-static raised floor when it will be able to play a good anti-static effect? People wear anti-static shoes and anti-static mats, anti-static composite sheet or anti-static raised floor does not necessarily play a good anti-static effect. Usually people wear socks and cushions. The young people's feet are prone to sweating. These socks and cushioned insoles can also conduct static electricity. However, due to the dryness of the shoes during the dry season in middle and old aged people, the socks and cushioned insoles cannot lead. Static electricity, and many manufacturers only require workers to wear anti-static clothing and anti-static shoes, ignore the adverse effects of socks and insoles, making this anti-static shoes and anti-static ground can not play anti-static effect. Therefore, a “human body comprehensive resistance tester†is placed at the entrance of the machine room or factory building. It can quickly and accurately detect those who wear unqualified antistatic shoes, socks, and cushioned insoles.
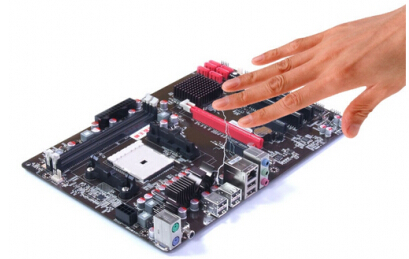
1) The thin oxide layer is broken down;
2) The leakage current density is high, causing the conductor to melt;
3) Increased leakage current causing premature failure and functional breakdown of the device due to changes in breakdown voltage. Although the interior of the electrostatic sensitive device has been protected, this is only effective when the charge transfer is limited to a certain size and continues for a certain period of time. According to test reports, electrostatic discharge damage is often only 1O% causing complete failure of electronic components at the time, usually as a short circuit, open circuit, and serious changes in the parameters, beyond its rated range, the device has completely lost its specific function; 90% will lurk down, causing a cumulative effect. Under normal circumstances, an ESD is not enough to cause the device to completely fail immediately, but there will be some degree of slight damage inside the component, usually expressed as a small deviation or drift of the parameters. The potential failure is not obvious and it is easily overlooked. If such components continue to work, with the increase in the number of ESD, the cumulative effect will become more and more obvious, the degree of damage will increase, and eventually lead to failure.
With the development of large-scale MOS circuits and placement devices (SMDs) and the development of component process technology, the energy sensitivity to electrostatic discharge (ESD) increases, and thin insulation layers can easily cause damage and failure. The electrostatic breakdown voltage of various types of semiconductor devices is shown in Table 1.
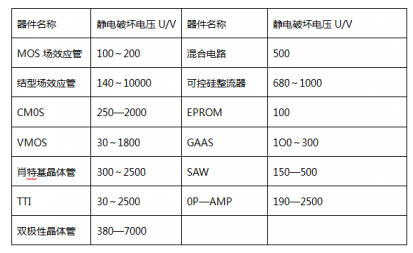
Table 1 Electrostatic breakdown voltage of semiconductor devices
From Table 1, we can understand the sensitivity of integrated circuits to static electricity. The difference of various chips lies in the different values ​​of 闽 voltage that they can withstand. In actual working conditions, a static voltage of 20V directly contacting the device is enough to destroy or reduce its performance.
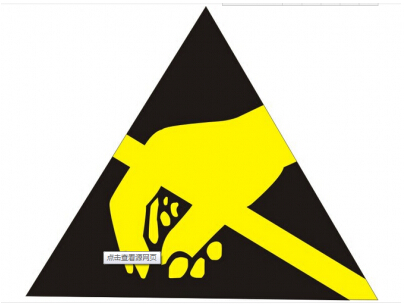
1) Electrostatic adsorption of dust in the air can easily lead to short circuit between the device leads;
2) Electrostatic discharge damage, so that the components can not be damaged;
3) Electrostatic discharge Electric fields or currents generate heat to damage components;
4) The amplitude of electrostatic discharge is very large. Electromagnetic fields with extremely wide frequency spectrum (from several tens of megabytes to several thousand megahertz and several hundred volts/meter of superposition) make electronic products damaged by electromagnetic interference.
5) The rework and repair of products damaged by electrostatic discharge will increase production costs and affect the economic benefits of the company.
In summary, electrostatic hazards exist in the entire process of electronic product production. The analysis result of electrostatic hazard in the production process of a certain electric shop is shown in Table 2. If the parts that are susceptible to electrostatic damage are controlled in the production process, the degree of electrostatic hazard in the production process will be limited to a minimum.
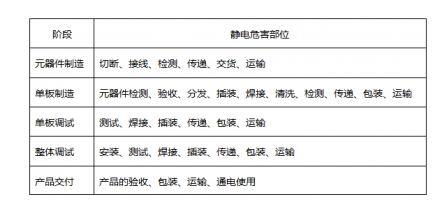
Table 2 Electrostatic hazards in the production process of a certain electric shop
Industrial anti-static measures
1, the degree of environmental hazard control; 2, process control; 3, grounding; 4, increase the humidity; 5, antistatic additives; 6, electrostatic neutralizer; 7, to strengthen electrostatic safety management.
The most effective measure is to allow people to "connect" or "ground" with the earth. Therefore, people should wear anti-static shoes. To keep the human body connected to the earth, this requires that the ground is also anti-static, so that the static electricity of the human body can be introduced into the earth. Therefore, the ground can use anti-static mats, anti-static composite sheets, and use anti-static grounding wire to connect well, such as funds Adequate use of anti-static raised floor, especially in the planning and design of the engine room plant can consider the use of anti-static raised floor, if the computer room plant is set and the equipment has been installed, but do not want to install anti-static equipment when the production of these equipment to stop production When it is time to influence, choose an anti-static floor mat that is inexpensive and easy to construct, anti-static composite sheet, etc.
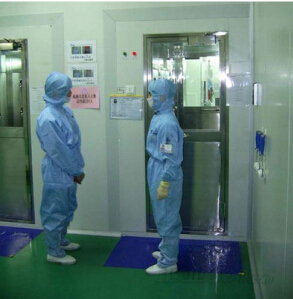
2020 hot sale 50w 100w 150w cob grow light, waterproof IP67, use Epistar 50w cob flip chip, pink lighting/3500k white lighting for you to choose.
50w 1pcs cob chip, can replace hps 300w;
100w 2pcs cob chip, can replace hps 500w;
150w 3pcs cob chip, can replace hps 1000w.
Waterproof Best Cob Led Grow Light, is your best choose for indoor plants, each lamp with bracket, easily install.
50w:
100w:
150w:
Cob Led Chip,Best Cob Chip,Led Cob Chip Grow Light,Cob Chip On Board Technology
Shenzhen Wenyi Lighting Technology Co., Ltd , https://www.szwygrow.com