The ring die and press roll are the heart components of the pellet machine. During operation, the ring mold is rotated by the motor, and the pressure roller rotates due to the friction between the ring mold and the material and the friction between the material and the pressure roller. Ring die and pressure roller
Ring die granulators are widely used in the feed industry, new energy technologies and pharmaceuticals, while ring molds and press rolls are key components. During the granulation process, the material is formed through small holes under the forced extrusion of the ring die and the pressure roller, so the working performance of the ring die and the pressure roller directly affects the forming rate and particle quality of the material. It is an indisputable fact that the domestically produced ring die has a short service life. The mechanical properties of the ring die are important factors affecting the service life of the ring die, and the mechanical analysis of the ring die is of great significance.
1. Analysis of forming process
The ring die and press roll are the heart components of the pellet machine. During operation, the ring mold is rotated by the motor, and the pressure roller rotates due to the friction between the ring mold and the material and the friction between the material and the pressure roller. The rotation of the ring die and the pressure roller causes the material to be forcibly extruded. Finally, the material is extruded in a column shape from the ring die hole, and then cut into a certain length of particles by a fixed cutter mounted on the outside of the ring die, as shown in FIG. Schematic diagram of ring mode particle mechanism
The particle forming process of the ring die granulator is based on the existence of a gap between the powder and granules. Under the action of temperature, friction and squeezing force, the powder shrinks the voids of the powder and granules to form particles with a certain density and strength. According to the different state of the powder in the extrusion process, the powder is divided into three zones, namely the feeding zone, the deformation pressing zone and the extrusion forming zone, as shown in FIG. (1) Feeding area: The material is basically not affected by the mechanical external force, but it is affected by the centrifugal force (rotation of the ring mold), so that the powder is closely attached to the inner ring of the ring mold. (2) Deformation pressing zone: With the rotation of the die and the roller, the material enters the pressing zone and is pressed by the die roller, and the relative displacement between the powders occurs. As the squeezing force is gradually increased, the interparticle voids are gradually reduced, and the material is irreversibly deformed. (3) Extrusion zone: in the extrusion zone, the die roll gap is small, the pressing force increases sharply, the contact surface area between the powder and granules increases, resulting in better bonding and being pressed into the die hole. .
2. Mechanical model of extrusion process
Obviously, the external forces of the materials in the three regions are different, and the force exerted by the ring mold in the circumferential direction is also different. The force conditions on the inner surface of the ring mold located in the three regions are analyzed below.
2.1 Feeding area
The material is basically unaffected by the mechanical external force, so it is considered that the ring mold of the feeding zone is not affected by the force.
2.2 Extrusion zone
The inner surface of the ring mold located in the extrusion forming zone is subjected to the same force as that at the entrance of the die hole, and the die hole is subjected to a force model, as shown in FIG. 2 . Where: P - pre-tightening pressure (N / mmz); v - material Poisson's ratio; r - die hole radius particle mechanism grain machine particle mechanism
At the inner side of the ring mold at 19.167 mm, the inner surface of the ring mold is subjected to a large force, and the maximum is 20.8 MPa. From the inner side of the ring mold 19.167 mm to the outside of the ring mold, the inner surface of the ring mold is subjected to a small force with a minimum value of 6.8 MPa. As shown in Fig. 8, in the deformation pressing zone, from the inner side of the ring mold to 19,167 mm from the inner side of the ring mold, the inner surface of the ring mold is subjected to a large force of 20,4 MPa. From the inside of the ring mold 19.167 mm to the outside of the ring mold, the inner surface of the ring mold is subjected to a small force, and the minimum value is 8.2 MPa. As shown in Fig. 6 and Fig. 8, the stress applied to the ring mold gradually decreases from the inner side to the outer side regardless of the extrusion forming zone or the deformation pressing zone. As shown in Fig. 7 and Fig. 9, the displacement of the inner surface of the ring mold changes linearly in the extrusion forming zone or in the deformation compacting zone, and the displacement of the outer side of the ring die changes greatly. The outer side of the inner surface of the ring mold is subjected to a small pressing force, which causes a large wear on the inner side of the ring mold and a small wear on the outer side of the ring mold. Ring mold particle mechanism granule ring die particle mechanism
The actual wear photo of the ring die, as shown in Fig. 10, the wear of the ring die and the pressure roller is irregularly worn along the axial direction, and the wear of the pressure roller and the ring die is severely worn at both ends, and the intermediate wear is less.
The comparison between the finite element analysis results and the actual wear conditions confirmed that the load is not evenly distributed in the axial direction of the ring die, and there are more materials on the outer side of the ring die, resulting in greater wear on the outer side of the ring die.
As shown in Fig. 6 and Fig. 8, the ring mold stress is relatively stable from the axial direction of the ring die at 38.3 mm, and the outer wear of the ring die is not more than the middle of the ring die. This shows that the r material is evenly distributed along the axial direction. Helps improve the wear of the ring mold.
4.2 Ring Mode Circumferential Stress and Displacement Analysis Ring Model Particle Mechanism Granulator
As shown in Fig. 11, the inner surface of the ring mold is 38.3 mm from the inner side of the ring mold, and the circumferential angle of the abscissa is calculated by the central angle of the ring mold, and the position of 00 is the closest to the ring mold and the pressure roller. And then through the extrusion zone, the deformation compression zone and the feed zone. Since the force received by the ring mold is symmetrical in the circumferential direction, half of the ring mold is taken for the curve.
Because -1
5 Conclusion
The force model of the inner surface of the ring die was established. The finite element analysis of the ring die was carried out by ANSYS. The analysis showed that: (1) the material is non-uniformly distributed along the inner surface of the ring die, and the material is distributed on the outer side. many. (2) The main reason for the serious wear on the inner side of the ring mold is that the ring mold is a cantilever beam structure; the main reason for the serious wear on the outer side of the ring mold is that the material is more on the outer side of the ring mold; the uniform distribution of the material layer along the axial direction of the ring mold is beneficial to Improve the wear of the ring mold. (3) Fatigue fracture is a failure mode of the ring mold.
Futong New Energy produces and sells biomass molding machinery such as wood pellet machine and straw briquetting machine. "target=_blank> mechanical equipment, and we also have a large amount of biomass pellet fuel.
Http://news.chinawj.com.cn
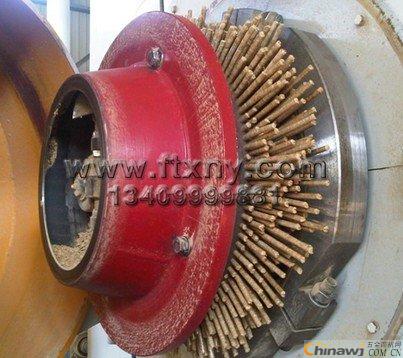
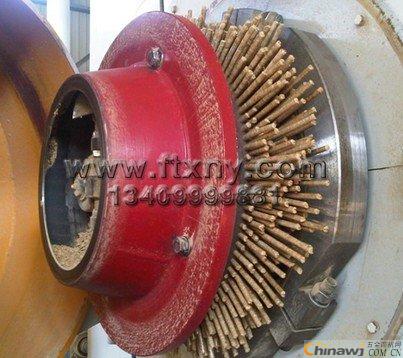
Strip clean disc is a new kind of Nylon fiber abrasive tools, can be the best substitute for traditional abrasive tools such as shutters and wire brushes.It is based on high-strength & wear-resistant fiber mesh, and the resin elastomer and nylon fiber and emery are bonded together by special process.
high-quality emery through a special process to form a high strength, high wear resistant, honeycomb shaped grinding wheel
solder joints, rust, sealant, scale, oxidation and other surface contaminants. Poly strip disc wheel an ideal tool for surface treatment such as paint, rust, and scale removal
wear resistance, strong water resistance, strong plasticity and good softness. Dirt will not block the fine seams of the grinding
surface, no rust, no fall off, low grinding sound and less dust
The strip clean disc network structure has the following characteristics:
1. Does not damage the surface of the object
2. The grinding force is uniform, and the grinding effect is uniform
3. Abrasion resistance, strong water resistance
4. Strong plasticity, good softness, suitable for various shapes of objects to be ground.
5. The dirt does not block the surface of the abrasive tool, there is less shedding, less noise, and less dust.
We distributes and wholesales various brands of Bonded Abrasives , Abrasive Sanding Disc, Cutting Wheels , Abrasive Flap Disc , Flap Wheels , Flap Disc Backing Pad, Flap Disc Adhesive , and Surface Conditioning Product etc, and enjoy a high position among consumers.
Clean And Strip Disc,Shaft Flap Wheel,Shank Mounted Flap Wheel,Keying Flap Wheel With Shaft
Zhengzhou Jiading Abrasive Manufacturing Co.,Ltd , https://www.jd-abrasives.com