The engine is the core component of the car and the core part of the cost of the enterprise product. In recent years, with the implementation of stricter emission and energy consumption regulations and the market's demand for energy saving and environmental protection, the competition for new energy power of automobiles has been upgraded. The traditional power gasoline engine and diesel engine technology have been continuously innovated, and engine replacement has been carried out. It has become an urgent need and conscious action of enterprises.
However, the construction of large-volume engine production lines is much higher than that of building automobile assembly lines. The quality control of production lines and the processing accuracy requirements of cylinder heads are much higher than those of assembled vehicles, especially for large-scale production of new engines. There are also technical risks and market awareness and promotion risks. China's auto industry has gone through many detours in the scale of plant construction and factory design, and has paid a high price, and some even endangered survival. Therefore, how to achieve "synchronization, modularization, flexibility, and leanness" in engine production is particularly important.
Evolution of engine construction methods
1. Large-scale production of rigid production lines
Before the 1990s, the single-type, high-volume production line model first advocated by Ford of the United States was still popular. Most of the new or expanded engine production lines were rigid production lines TL (in accordance with mass production methods). Transfer Line). Due to the long life cycle and single product of the engine products at that time, the focus of the process design was mainly on how to ensure the accuracy of the machining and further improve the production efficiency.
2. Flexible production line
In order to solve the variant production of the product and to facilitate the replacement of varieties, flexible production technology has been introduced into automobile production. Since the 1980s, the exchangeable spindle box machine tools, machining centers, and CNC special machines have become more and more important in the production line. The flexible production line FML/S (Flexible Manufacturing Line/System) is another revolution in engine manufacturing technology. Its outstanding feature is that the production line has flexibility, which can realize the processing of the same technology platform products or the processing of similar products. The disadvantage is that the initial investment scale of the equipment is large, and the production efficiency is also limited.
3. Agile lean flexible production line
In order to solve the contradiction between engine diversity and economy, meet the needs of variable varieties and variable batch production, and further improve the production efficiency of flexible production lines, the agile flexible production line AFTL (Agile Flexible Transfer Line) began to introduce engine production, its main goal Yes:
(1) Respond quickly to changing market demands.
(2) To meet the needs of automobile engines "multi-variety, variable batch, high efficiency, low cost".
(3) Compliance with the principle of “lean production†– to maximize economic benefits with minimum investment.
Engine lean construction mode
The lean production method combines the advantages of mass production and small batch production methods, and strives to achieve low-cost production of multi-variety and high-quality products in mass production. The lean construction mode is already the consensus of the automobile manufacturing industry. At present, among the domestic passenger car companies, Guangzhou Honda has embarked on a typical development path of “market-oriented, less investment, faster output, and rolling developmentâ€. Dongfeng Honda Engine Co., Ltd., which was jointly developed, was put into production in 1999. At the beginning, the annual production capacity is only 30,000 units. After 60,000 units, 120,000 units, and 240,000 units, the annual capacity has been expanded to 360,000 units. The production line can alternately produce 1.3 to 2.4L. Class 5 engine. The new construction of commercial vehicle enterprises also adopts a batch-and-roll development model, with the model of “one-time planning, step-by-step implementation, and rolling development†as the lean construction policy.
The EQ4H engine is a general term for EQH145-30, EQH160-30, EQH180-30, and EQH200-30 engines produced by Dongfeng Commercial Vehicle Engine Factory (see Figure 1). These four engines are independently developed by Dongfeng Commercial Vehicle Technology Center and have completely independent intellectual property rights. They are all four-stroke, water-cooled, in-line four-cylinder, supercharged intercooled, electronically controlled common rail diesel engines with rated power of 107/2 400 respectively. , 118/2 400, 132/2 400, 147/2 400kW/(r/min), using BOSCH high pressure common rail fuel injection system, the emission reaches the national III level, with the potential to upgrade to the national IV. As the core power of Dongfeng Commercial Vehicle Company's Tianjin (D530) truck, its power, economy, reliability and other indicators are at the forefront of similar products.
figure 1
Metallographic Mounting Machines
Hot mounting is ideal solution to get high quality, uniform size sample,as Well as short process time. lt is to use mounting compounds With certain pressure, temperature to make a sample.
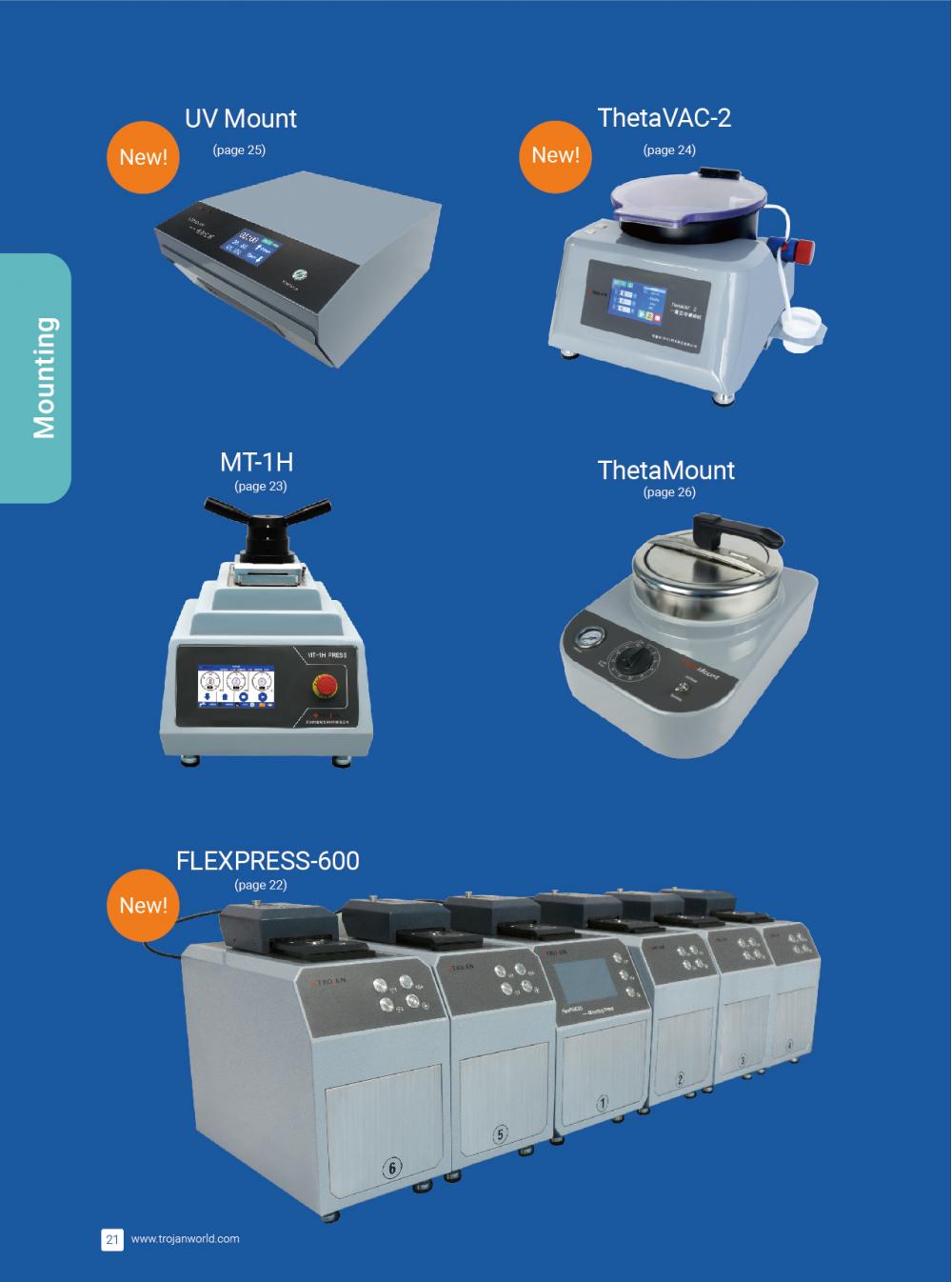
Metallographic Mounting Machines,Mounting Specimen Preparation,Metallography Analysis Mounting,Metallurgical Sample Preparation Equipment
TROJAN (Suzhou) Technology Co., Ltd. , https://www.trojanmaterial.com