2 Technical characteristics
2, 1 Positioning is accurate, clamping is reliable SPACE, EXPRESS body except for some skeletons using profiles, the other parts are stamping parts and rolling parts, the assembly precision between the parts is high, so the technology of the body group welding tire The level requirements are also higher. The "modern" passenger car body welding fixtures have taken this into consideration in the production. From the tire frame, the tire panel to the fixture and the positioning block, they are carefully designed, carefully manufactured, carefully installed and carefully adjusted. After the equipment is adjusted, the laser is measured. Instrument inspection, the general part positioning block size accuracy is about ± 0, 3 mm, the key parts such as the positioning pin size accuracy is about ± 0, 05 mm, far higher than the current domestic use of the combined tire positioning accuracy.
Due to the fine production of the components of the combined tire and the pneumatic driving method, the “modern†bus body welding fixture is positioned accurately during operation, and the fixture moves quickly and forcefully, and the work is reliable.
2, 2 power source centralized, effective
The body-mounted tires used in the passenger car industry now have various forms of power, such as electric, pneumatic and hydraulic transmission. Most of the equipment for driving the tire frame is driven by hydraulic transmission or electric mechanical transmission. The driving of the clamp and the movable positioning block generally adopts pneumatic transmission, and the control system basically adopts electronic or electrical control. Most passenger car tires use three power sources at the same time, and electric, pneumatic and hydraulic transmissions are commonly used.
The “modern†bus body welding fixtures use one type of power, namely pneumatic transmission. Whether it is the movement of the front group welding tires or the left and right surrounding welding tires, or the lifting of the floor group welding tires, or the movement of the fixture, the movable positioning block, or the operation of the control system, the compressed air is used as the power source. . Compared with electric systems and hydraulic systems, pneumatic systems are simple in structure, good in usability and maintainability, and have low investment. Because the power of the equipment and the power of the control system are all compressed air, the "modern" bus body welding fixtures are simple to operate, reliable in work and safe in construction. As shown in Figure 3.
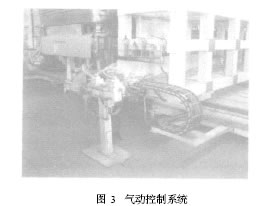
2, 3 flexible position, fast SPACE, EXPRESS passenger car is two models of different body length, height, wheelbase, window distance, in order to simultaneously adapt to the online mass production of these two models, the front wall assembly of the combined tire The welding tire, the floor skeleton assembly group welding tire and the left and right side assembly group welding tires are specially designed.
In the length direction, the rear wall assembly of the two models is fixed in the group welding tire, and the change in the length direction is on the front group welding tire. When working, the front wall assembly is placed on the movable table. After positioning and clamping, the cylinder is driven from the rear to the rear to send the welding position, and the control valve is used to control the feeding distance to adapt to different models. The front wall assembly welding fixtures on the two side tire panels are in the longitudinal direction. Designed as a mobile structure driven by a cylinder.
In order to adapt to the change of the height of the vehicle body, the clamp of the top longitudinal beam also adopts the mobile structure driven by the cylinder, and the floor skeleton is designed with two sets of positioning blocks, one set is a fixed positioning block and one set is a movable positioning block. The low body is fixed by the positioning block. When the high body is produced, the cylinder drive gear and the rack device are used to raise the movable table to the high position. Then the cylinder is used to drive the movable positioning block to reverse the positioning, and then the movable table is lowered back to the already The welding operation is performed on the raised active positioning block. As shown in Figure 4.
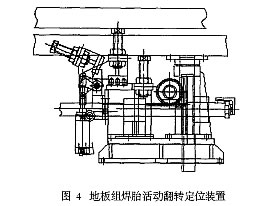
2, 4 spacious, convenient for welding. After the "modern" bus body welding fixture is opened, the distance between the two sides of the welded tire tire panel reaches 5 200 mm, even if the two sides are closed in place, the distance between the two side panels It is still kept at 3 600 mm, so it is flexible when clamping the left and right side surround assemblies, the floor frame assembly and the front and rear perimeter assemblies. It is also convenient to weld on the outside of the body when welding the body.
3 Working principle
First, set the front group welding tires, the left and right surrounding welding tires, fixtures, etc. in the open (release) state, and then proceed as follows:
(1) The left and right side frame assemblies are respectively hoisted on the left and right side group welding tires, and then clamped after positioning.
(2) Lift the floor group welding workbench to a high position, and hoist the front, middle and rear three-story skeleton assembly and the rear five-seat skeleton assembly to the movable workbench for positioning and clamping, and then work on the activity. The table is lowered back to the working height, and the joint between the segments is welded by a CO2 protective welder.
(3) Open the left and right side group welding tire activity table drive cylinders, so that the left and right side circumference assemblies are joined to the floor frame assembly, and the joints are welded.
(4) Hanging into the rear wall assembly, aligning the rear waist joint connecting beam with the side wall assembly lug connecting beam port, and starting the rear wall assembly group on the left and right side group welding tire panels The welding fixture is used to tightly connect the rear wall assembly to the side wall assembly and weld the connecting plate.
(5) Lift the front wall assembly into the workbench of the front wall group, position and clamp, start the propulsion cylinder and send it to the welding position, and then start the front wall of the tire panel on both sides. The welding fixture clamps the front wall assembly to the left and right side circumference assemblies.
(6) Lift the large top assembly and clamp it after positioning.
(7) Body assembly welding.
4 Conclusion
Due to its advanced design, well-made and easy operation, the “modern†bus body welding fixtures have a high level of flatness and high production efficiency, which is playing an increasingly important role in the business activities of the company.
Previous page
Pneumatic Tools,Pneumatic Air Tools,Pneumatic Screwdriver,Pneumatic Power Tools
NINGBO AOCHENG IMPORT AND EXPORT CD.,LTD , https://www.aulceln.com